Extending a drill with a tube is an option I use.
HSS drills become weak when heated by a TIG torch. That is the reason you do not want to weld at the border of the tube where the drill slips in.
A quick and proper solution is shown here, just slide the drill in and apply a short and heavy pulse. This way the drill is fixed with minimal material change and the shaft takes care of drill bending forces.
This example is a 4 mm HSS drill in a 6 mm 304 steel tube. What you see is one of two welding spots. Total needed operational length: ~200mm. You may want to do the welding spots at different cross sections heights in order to reduce influence of material properties, in order to achieve a better torque rate.
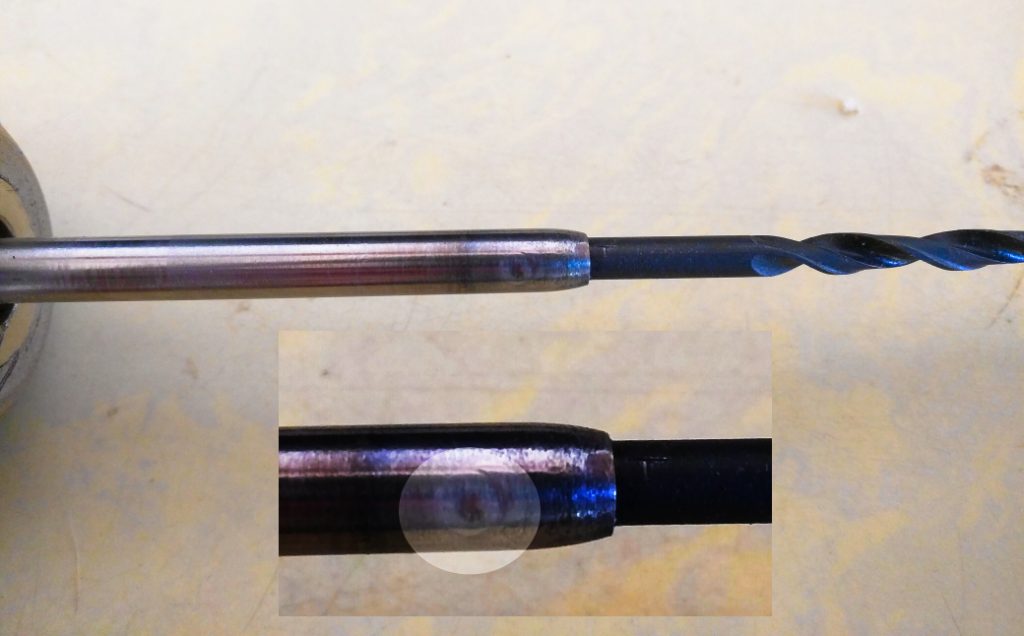